THE TOUR ENGINE IS A PATENTED, SPLIT-CYCLE, INTERNAL COMBUSTION ENGINE THAT STANDS TO DELIVER SUBSTANTIAL EFFICIENCY GAINS THROUGH SUPERIOR THERMAL MANAGEMENT
Unlike current combustion engines, which use the same cylinder for all four strokes (intake, compression, combustion, and exhaust), Tour’s patented engine design splits the conventional 4-stroke cycle between two cylinders: the compression cylinder hosts intake and compression, and the expansion cylinder hosts combustion and exhaust.
A PROPRIETARY CROSSOVER VALVE IS USED TO TRANSFER THE COMPRESSED
CHARGE FROM THE COMPRESSION CYLINDER TO THE EXPANSION CYLINDER.
This thermal management strategy reduces the magnitude of the two major efficiency losses in
conventional 4-stroke engines – heat loss to the coolant/oil and exhaust energy loss.
The end result is a thermally optimized engine that, according to advanced computer simulations and working prototypes, can achieve up to 30% greater efficiency—significantly reducing both fuel costs and noxious emissions. Even better, Tour Engines utilize the same “block and piston” architecture that has been at the heart of ICEs for over a century, ensuring they are cost-effective to manufacture, adopt, and maintain.
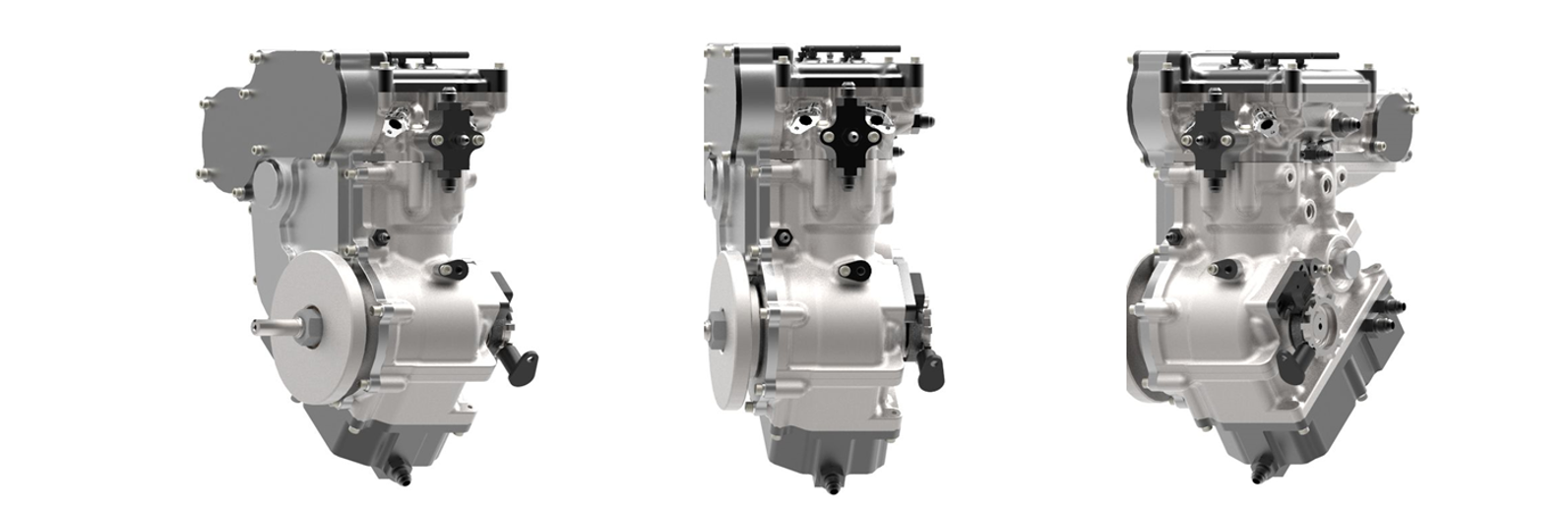
Learn more about Tour ENABLE
REIMAGINE THE FUTURE WITH TOUR ENGINE
Tour is backed by sophisticated technology investors and has won grants from both the US DOE’s ARPA-E and The California Energy Commission (CEC) and Israeli (DOE) governments. Tour has also been issued 48 patents (US and International) with more pending.
LEARN ABOUT MORE WAYS YOU CAN GET INVOLVED WITH OUR TEAM
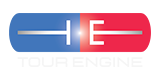